Former US Airways Site at PIT Gets Second Life
Florida-based FJ Turbine Power Inc. to test aircraft engines at restored maintenance site
By Natalie Fiorilli
Published August 10, 2020
Read Time: 5 mins
A Florida-based company plans to start testing aircraft engines at Pittsburgh International Airport, after refurbishing a rare aircraft maintenance facility built during its hub days.
The site, located across the airfield, adjacent to what are now American Airlines maintenance hangars, is a former aircraft engine test cell building left behind by US Airways.
That hidden gem stood out for a southern Florida-based company looking to expand its operations.
“In the country, there’s probably only around five test cells of this size in total,” explained Manny Castañedo, vice president of FJ Turbine Power Inc., an engine maintenance, repair and overhaul (MRO) business in Hialeah, Florida, near Miami.
The company acquired the former US Airways building in 2012. But having sat idle for many years, the team had a lot of work to do to refit the facility. Since then, crews have been working to obtain the necessary operating permits, secure financing, and restore other parts of the building.
Today, the site is undergoing the final system checks and other verifications required to be an FAA-certified aircraft engine testing center.
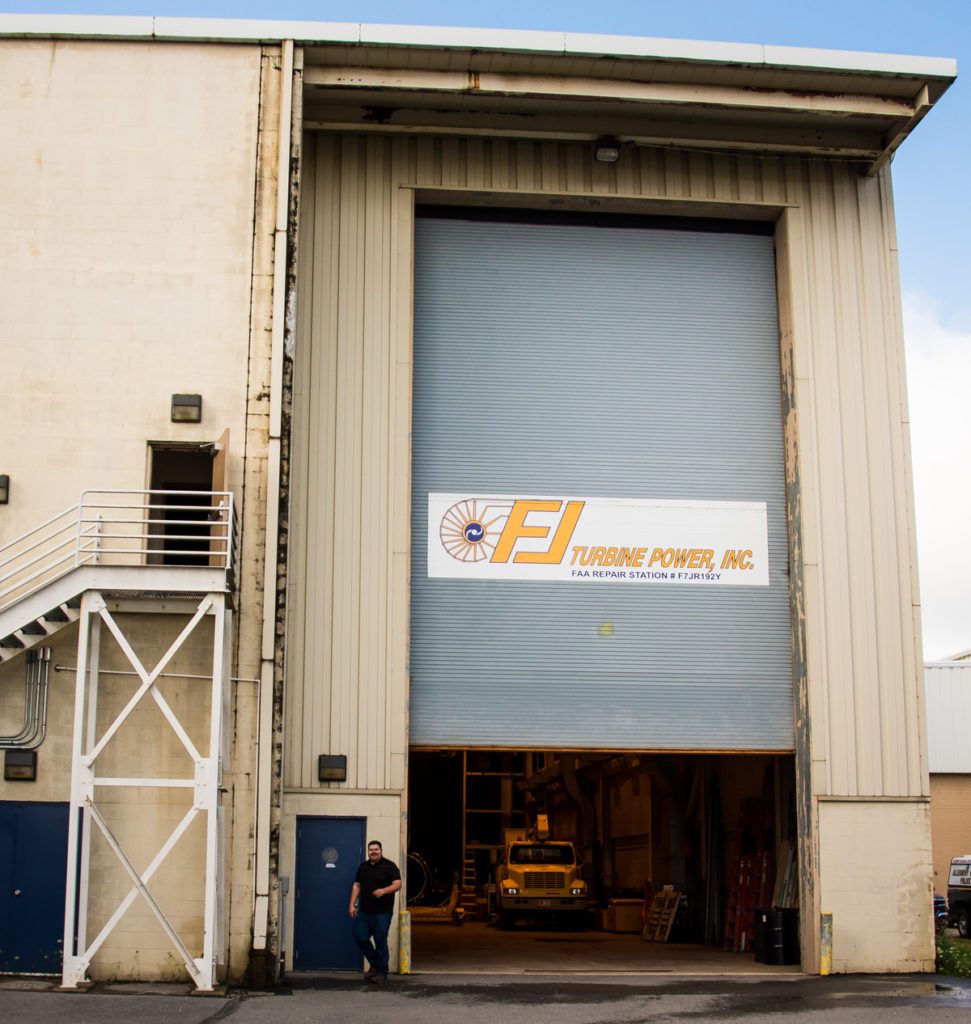
FJ Turbine Power Inc. is located near what are now American Airlines maintenance hangars at PIT. (Photo by Beth Hollerich)
“We saw a diamond in the rough. But, with a little polishing, labor and a lot of care and very resourceful people, we were able to get it to where it is now,” Castañedo said.
“Once we’ve proven ourselves here, we expect there to be a large increase in testing. Our goal is to eventually be working on 15 engines per month. But in the next couple of years, we hope to bring in more business and opportunities and show others how ideal Pittsburgh is as a central location for both air and land transport.”
Inside the Test Cell
From outside, the building looks like any other maintenance shop at an airport – but the moment you step inside, it’s clear that the newly restored test site is anything but.
Inside the main entrance, the ceilings are lined with an intricate series of hoists, used for lifting and moving aircraft engines that weigh roughly two tons. Below sits a large engine adapter, in which maintainers and inspectors can mount an engine to simulate its capabilities as if it were connected to the airframe of an aircraft.
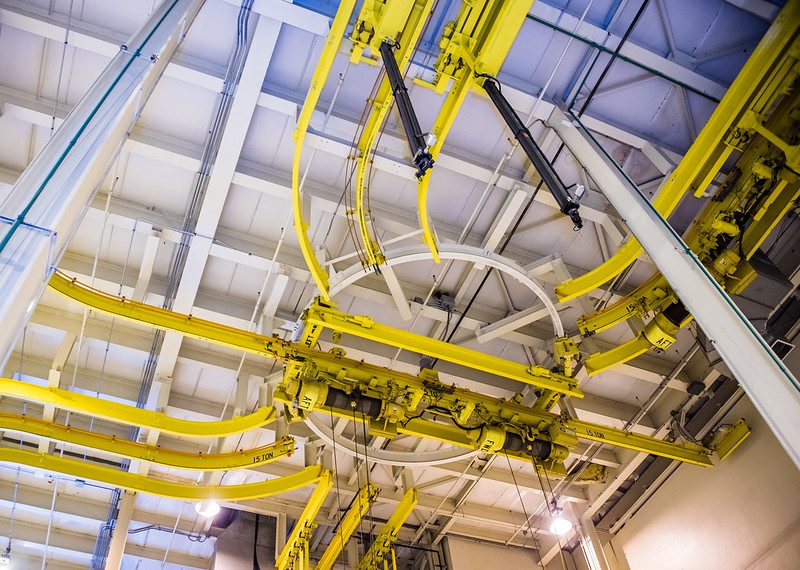
The ceilings are lined with a series of hoists to lift and maneuver aircraft engines. (Photo by Beth Hollerich)
The actual test cell is located in the next room.
An approximately 1,500 square-foot space, the test cell is large, open and almost noiseless. To enable sound suppression in the room, rubber seams help to separate the cell from the rest of the building.
The most noticeable feature of the cell, however, is a large round and funnel-like “augmenter” at the front of the room. The augmenter, which protrudes through the building to the outside, works to smoothly collect the exhaust coming from the engine during a test.
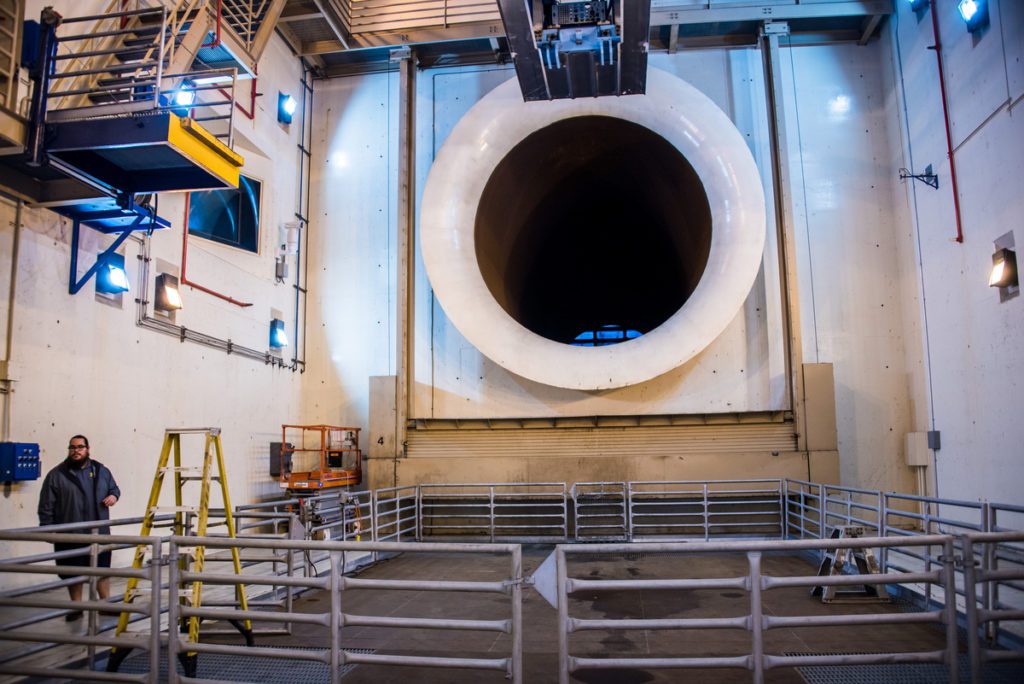
Inside the test cell, the funnel-like augmenter works to smoothly collect the exhaust coming from the engine during a test. (Photo by Beth Hollerich)
On the wall opposite of the augmenter, a series of “baffles” or screens serve the purpose of straightening the air before it goes through the engine.
“The goal of this room is to create, as best as possible, a linear flow of air that is smooth and without any inconsistencies,” explained Paul Anglin, a test cell inspector for FJ Turbine Power Inc. “If you have winds and other conditions, you’re not going to get an accurate result. In here, it’s a controlled environment that allows us to better test the engine.”
Using the building’s hoist system, Anglin and other inspectors are able to maneuver an engine into the test cell room and attach it to the adapter to simulate the engine as if it were attached to an aircraft.
(Video by Paul Anglin)
In another room upstairs, crews are able to operate the engine when it’s connected to the adapter inside the test cell, using what is called a Full Authority Digital Engine Control (FADEC) system.
From there, they can test an engine capable of producing up to 90,000 pounds of thrust to its full takeoff power. Along with controlling the engine, the FADEC system provides a full range of data and diagnostics information, displayed on monitors for the maintainers and inspectors to evaluate.
“You have a mechanic as the operator, physically running the engine and then an inspector that is monitoring the different parameters you’re looking to examine,” Anglin explained. “It’s basically the same experience as if you were inside the cockpit.”
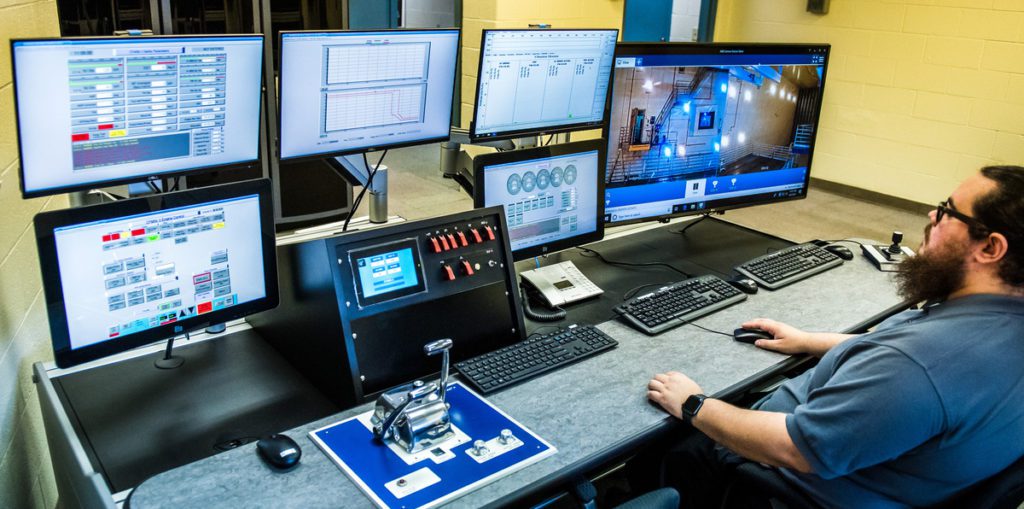
A Full Authority Digital Engine Control (FADEC) system allows crews to operate the engine and monitor a full range of data and diagnostics information. (Photo by Beth Hollerich)
What’s Next?
The test cell is capable of testing a variety of engines. For now, the site will mainly focus on testing CFM56 series and CF6-80 engines, which are used on the Airbus A320 family and Boeing 737 aircraft, to name a few.
In addition to working with a number of airlines located in the Americas and Europe, the company will perform engine maintenance and testing for cargo operators and aircraft leasing companies, among others.
Once the final system checks and certifications are complete, the site will be operational.
“We’re at the finish line,” Castañedo said.